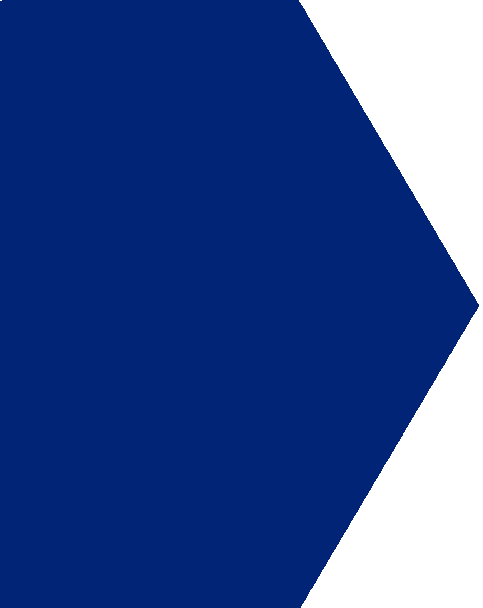
Get the Digital Power from your Textile Rotary Printing Machine by using Fully Loaded 3rd Generation NEO+ Screens
GURJAR NEO+® Third Generation Screens are available in Mesh counts of 135 ED,165 ED, 195 ED and 195 S. Benefits of using Gurjar NEO+® Third Generation Screens:
- Higher open area, Larger Holes and Increased Screen Wall Thickness
- The highest printing resolution in textile rotary printing
- Improved surface printing due to very high Open Area
- Benefits in half-tone and geometrical printing with more effective biconical hole shape
135 ED Mesh NEO+® Screen
This screen has the highest open area and the widest hole size with optimal thickness, therefore allowing substantial amount of paste to pass through. This screen is flawless for achieving even coverage and achieving great results while using white/gold/ metal pastes.
165 ED Mesh NEO+® Screen
This screen is the optimal standard for a broad range of applications from fine lines to blotches.
195 ED Mesh NEO+® Screen
The higher the mesh count, the finer you can print. This perfect combination of higher mesh count and proportionately higher hole size, with maintaining optimal thickness, guarantees high quality results for half-tone, geometrical, fine lines, multi-colour and biconical hole designs printing.
195 S Mesh NEO+® Screen
This screen has an open area of 20% thus applicable for achieving superior results in prints with higher resolution and voluminous substrates i.e.
- Half tones : higher resolution of the shade impressions
- Geometrical/ Fine lines : the straightness of the printed shapes edges is improved
- Reactive printing : achieving voluminous paste transfer thus the supericial unprinted spots after washing will be avoided
REPEAT | 640 | 640 | 640 | 640 |
---|---|---|---|---|
MESH | NEO+ 135ED | NEO+ 165ED | NEO+ 195ED | NEO+ 195 S |
PKG | 10 | 10 | 10 | 10 |
Screen Parameters
To fully understand the benefits of the NEO+ range of screens, one must appreciate the general screen characteristics – The open area, mesh count and screen thickness – they all have a close relation.
This is due to the nickel growth occurring during the screen manufacturing process. Simply put, a higher mesh count and a higher thickness of the screen decreases the open area. During the screen making process, the nickel grows from the mandrel in both directions, to the top and to the sides.
Using the expertise in electroforming chemistry gathered over more than 50 years, GURJAR Screens is able to steer the nickel growth mainly in the top direction. This way, the dam shape stays thin and gets streamlined. Therefore the ratio between the hole-size, mesh count and thickness of the screen can be pushed beyond the conventional boundaries of the rotary screen-printing industry.
With the dam width decreasing and higher open area improves the screen’s printability exponentially. Less printing pressure is needed to achieve a decent coverage of the substrate. Therefore the new NEO+ range of mesh screens can even save paste consumption and are more cost effective in comparison to other generation mesh screens. These screens are best suited for full penetrative printing as well as surface printing, both providing the best possible printing resolution in textile printing.